Blog
Lithium-ion batteries are moving from ground to sky. That changes everything.
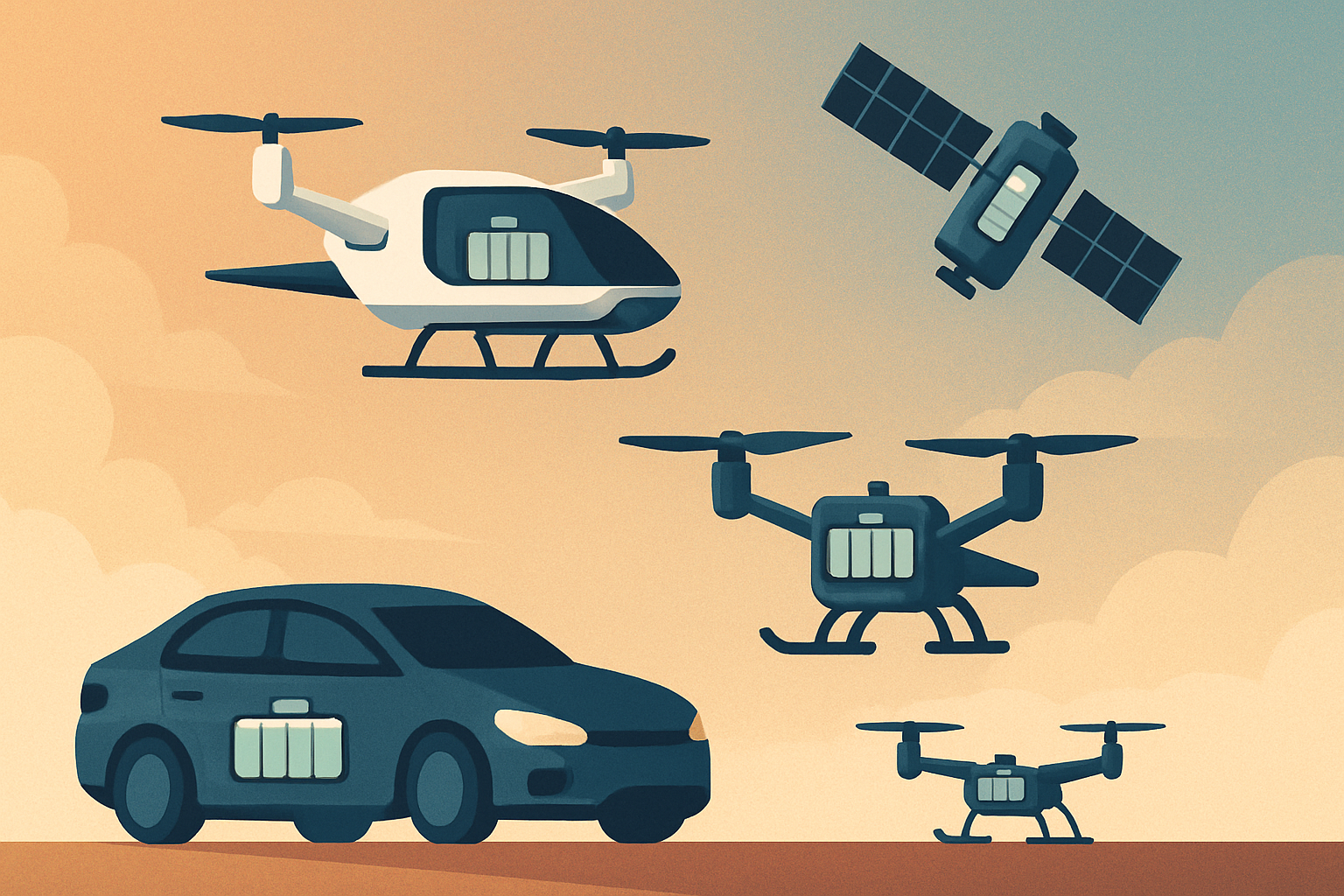
Over the past decade, lithium-ion battery innovation has been defined by one thing: cars. The electric vehicle (EV) boom, fueled by government incentives, consumer demand, and global urgency to address climate change, has shaped how people think about battery innovation.
But lately, there’s been a noticeable shift in where the most strategically important opportunities are headed. And they’re no longer on the ground; they’re in the sky.
This change isn’t just about technology. It’s also about politics, economics, and national security. With the new administration in the White House, federal priorities are evolving; we’re already seeing signs that the U.S. battery strategy is pivoting from a “climate imperative” to “national security imperative”—but still an imperative nonetheless. The Inflation Reduction Act (IRA) and Bipartisan Infrastructure Law (BIL), which helped turbocharge domestic EV manufacturing, are being reevaluated. While some elements of these laws may survive, it’s clear that the Trump administration plans to steer investment toward defense and aerospace rather than electric cars.
The climate crisis hasn’t gone anywhere. In fact, it’s more urgent than ever. But now a new, second spotlight is shining on our need to support our soldiers, international allies, and strategic global interests.
This shift was recently covered in The Electric, noting that the Trump administration is continuing supporting battery development—but the priority is the air, not the ground. Mass-market EVs may no longer be the star of the show. Drones, electric vertical takeoff and landing (eVTOL) aircraft, and other aerospace platforms are now commanding center stage.
So what happens when lithium-ion batteries go from Teslas to eVTOLs, from SUVs to satellites? The short answer: the entire set of technical priorities changes, and one overlooked part of the battery suddenly becomes critical.
Let’s rewind a bit. For the last 15 years, battery startups were laser-focused on improving electrodes, because in EVs, the name of the game was cost and range. Even incremental improvements like boosting a battery from 200 to 250 miles of range, or dropping the cost from $40,000 to $30,000, could increase market share by millions of drivers. And since electrodes determine how much energy a battery can hold and how cheaply it can be made, that’s where the action was.
It’s not a new problem. In fact, the very first car that Ferdinand Porsche ever worked on was the 1898 Egger-Lohner C.2 Phaeton—which ran on a hulking 1,000-pound battery that barely got 50 miles of range. For over a century, battery innovation has been about packing more energy in a smaller, cheaper box to make electric cars practical.
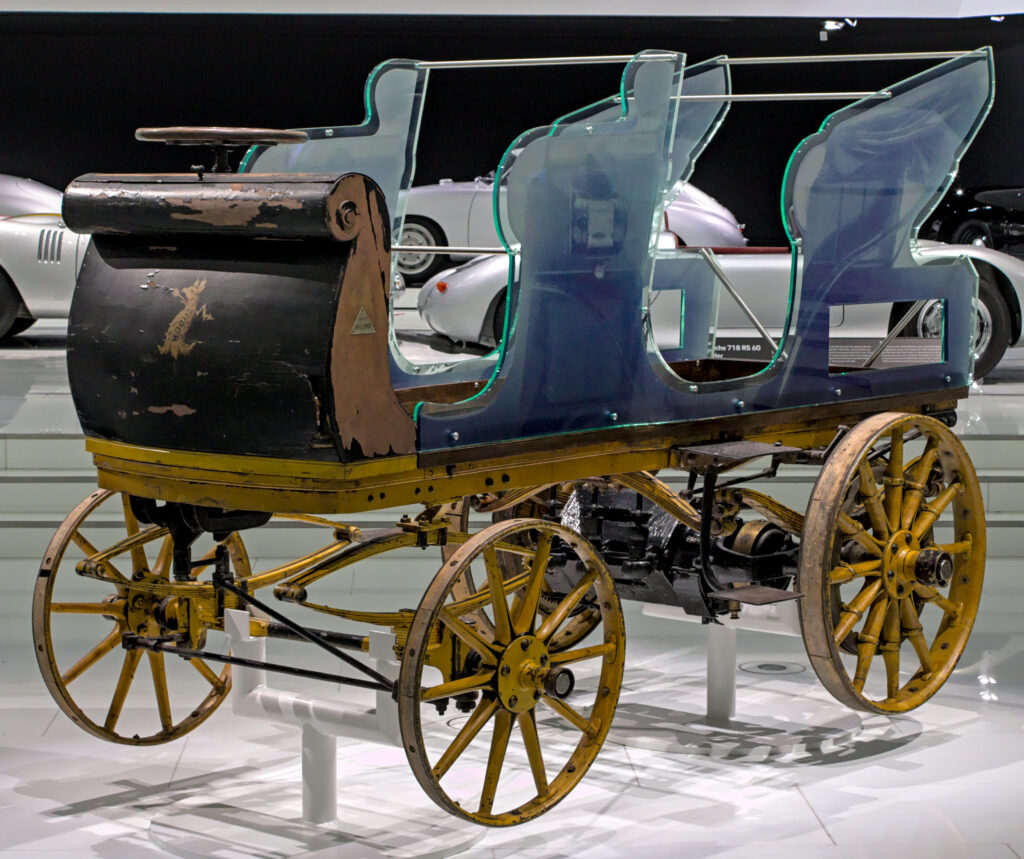
Now, priorities are poised to flip upside down. Range and cost, which dominated the EV era, become less important. In aerospace and defense, consumers aren’t demanding a cheaper product. And squeezing a few more miles range of an eVTOL or drone doesn’t meaningfully unlock new mission profiles.
Instead, a whole different set of performance metrics begins to matter: peak power (think: stable hovering), extreme safety (no onboard fires during crashes or under enemy fire), fast charging (turnaround time for missions), cycle life (to extend deployment time), and reliable operation in extreme temperatures (from Arctic cold to desert heat).
And all of those performance levers are dictated not by the battery’s electrodes—but by the electrolyte.
To be specific: electrolytes don’t really affect energy density or cost. Those are largely electrode-driven. But the electrolyte controls everything else: performance under extreme hot and cold, safety under abuse, charging time, peak power output, and cycle life.
This last one—cycle life—is critical for platforms like satellites, where swapping a dead battery isn’t exactly an option. You need the battery to work for years without measurable degradation, which means the electrolyte has to be rock-solid for the long haul.
Or take eVTOLs. These systems demand high power delivery for hovering and takeoff, robust safety to survive hard landings, and fast charging to ensure rapid turnaround time between flights. Every one of those performance levers runs straight through the electrolyte.
This isn’t a theoretical concern. After several well-publicized lithium-ion battery fires in the Boeing 787 Dreamliner, the most feasible solution was to physically encase the battery in a bomb-proof steel box. That worked, but it cut usable energy density of the batteries by nearly 80%. In other words, solving the electrolyte safety problem doesn’t just prevent catastrophic failures. It also frees up more of the battery’s energy to do useful work, effectively increasing range and performance.
So as lithium-ion moves from ground to sky, the strategic bottleneck is no longer the electrode. It’s the electrolyte. And that’s where Aionics is focused.
We’ve built the first AI-powered platform for designing application-specific electrolytes. Our closed-loop software/hardware platform, Ami, co-optimizes for all the performance metrics that matter in these new domains: thermal stability, safety, power delivery, and low-temperature performance. Already, we’re working with a defense-contracted aerospace company on a nonflammable lithium-ion cell. By making the electrolyte nonflammable, we break the chain reaction that leads to the super-hot battery fires we’ve seen engulfing EVs on the news. If the electrolyte doesn’t burn in the first place, the runaway chain reaction can’t start.
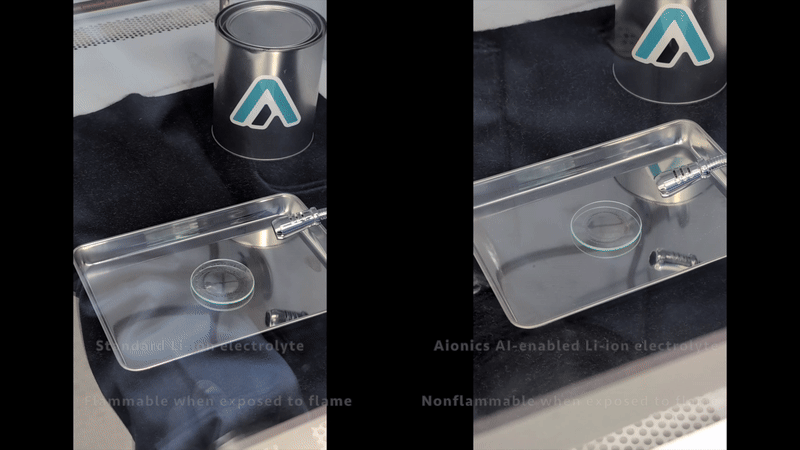
We’re also partnering with an American cellmaker on a high energy density battery that contains a special low temperature electrolyte that enables operation below -40°C. This is a critical need for the defense industry, which needs to be able to support missions in brutal Arctic tundra, and for which there is no solution readily available on the market. And our fast-charge optimization work in the automotive sector directly applies to mission turnaround times.
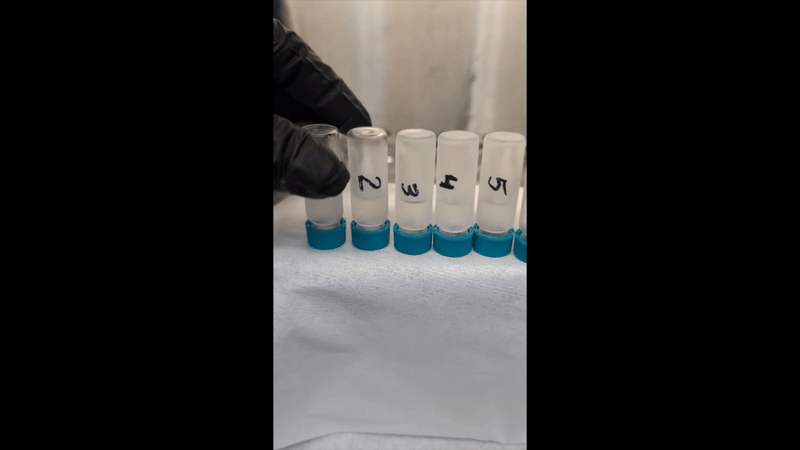
How are we bringing these cutting-edge solutions to market? We’re not building factories and we’re not manufacturing batteries. We’re focusing on the design step—creating high performance drop-in electrolytes for any cell form factor and use case, and bringing them into commercial production with our manufacturing partners. As NVIDIA has demonstrated in chip design, this model keeps us capital-efficient and laser-focused on innovation.
The electrolyte is about to have its moment. As battery applications move into more extreme, less forgiving environments, the demands placed on this once-overlooked component are rising fast. But most of the West is still playing catch-up. Our industrial base has been optimized for electrodes and mass-market EVs. But we need to start investing in the tech that enables the next generation of aviation, defense, and space.
At Aionics, we’re building that tech. And we believe the sky is just the beginning.
By
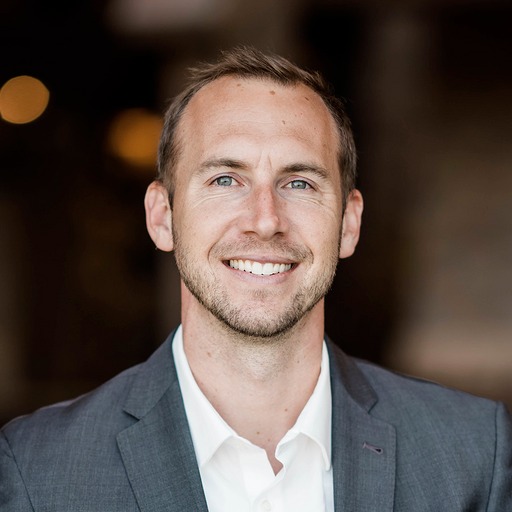
Chief Executive Officer
Newsletter Registration
Subscribe to our newsletter and stay updated with the latest from Aionics.